Operations managers first need to decide decide what to outsource. Outsourcing the wrong part of your product or service can result in poor quality, increased costs, and other mishaps. A poor outsourcing decision can result in key intellectual property being leaked or, worse, the creation of a new and fierce competitor.
An important part of product design is the manufacturing process. You need to consider how an item will be made when designing it. You can’t just design a product, throw it over a wall, and hope that the manufacturing people can figure out how to produce it.
Outsourcing creates the same issue. If you outsource, you have to design your supply chain at the same time. You also have to design the components of your product that you want to outsource so that they’re easy to outsource.
Most of the factors that make a component or product easier to outsource reduce the amount of communication necessary between your firm and the supplier. A number of them are listed here:
Legality: You can’t legally offshore certain things, such as certain defense-related technologies. This limits the choice of outsourcing partners to domestic suppliers. If you design your product to avoid such legal restrictions, the pool of firms you can outsource to is much larger.
Modularity: A component is modular if it has very few interconnections (electrical, physical, or informational) with the rest of the product. The more modular a component is, the easier it is to outsource. Tires are a great example of modularity because they have only three physical specifications. If they meet those specifications, they’ll fit the automobile. Everything else about tires is standardized.
Stereo speakers are similar. They typically have a single pair of wires that carries an electrical signal from an amplifier that is turned into sound. Speakers don’t need to be produced along with an amplifier and don’t need any electronics or software connectivity. Speakers can be designed pretty much independently of the amplifiers that provide the sound signal. The design doesn’t have any physical constraints.
Standards: A standard is an agreement by a number of firms to create an interface to the same technical published specifications. Examples of standards include the USB connector that people use to connect peripherals to computers and the electrical outlets in your house that you plug things into.
Standards make components easier to outsource because component makers don’t have to communicate or work with the outsourcing firm much because what they’re making is designed to universal specifications.
The beauty of standards is that it allows relatively complex interfaces between components to be agreed on without going into all the detail necessary to specify those interfaces that would be necessary if those standards did not exist. The use of standards combined with reducing the number of interfaces through modular design reduces the necessary information flow between your firm and the supplier, which makes components much easier to outsource.
Tribal knowledge: A lot of knowledge about how to produce a product never gets documented. The more of this tribal knowledge that a product has, the more difficult it is to outsource. One way to design for outsourcing is to try to include as much of this knowledge as possible in the specifications you send to your supplier. Another way is to substitute some standard for that tribal knowledge.
If you can’t answer no to these risks (or have a plan to deal with problem areas), you need to rethink any plan to outsource your product or service.
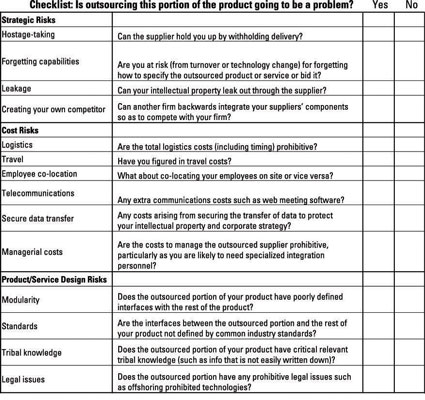