Most companies know that designing and maintaining a strong and reliable supply chain is vital to profitability and long-term survival. It is important to improve supply chain management through better communication, accountability, and inventory management.
Better communication
Through modern information technology, companies are now able to share two critical data points with their suppliers: actual customer demand and the amount of inventory on hand.
Fortunately, modern scanners used at retail outlets enable suppliers to access consumer demand instantaneously. Your local grocery store probably utilizes this scanning system — to tally your order and to facilitate stock-replenishment orders. That is, companies can use this point of sale (POS) information to trigger the ordering of inventory.
In addition, if suppliers can access a company’s POS data, they can anticipate when you’ll likely place an order before you actually place it! The bar coding of inventory facilitates this constant monitoring throughout the supply chain. Concepts such as collaborative planning, forecasting, and replenishment (CPFR) strive to increase supply chain integration by increasing the visibility of demand at every point on the supply chain.
Outsource inventory management
More and more companies are putting the responsibility of inventory management on their suppliers. This practice, known as vendor-managed inventory (VMI), is quite common in major retailers.
Here’s how it works: A major retailer gives a certain amount of shelf space in its store to a supplier, which keeps its products stocked there. Armed with the retailer’s POS data, the supplier can restock its products without direct involvement by the retailer. This saves the retailer time and money because it avoids the job of managing the inventory.
VMI requires trust in a supplier. For VMI to work, a company must give the supplier access to sales information so it can restock the shelves as necessary. In many cases, especially retail, the supplier also supplies competitor retailers. Given actual sales and inventory levels, the supplier could inadvertently provide sales data to the competition. So trust and integrity are necessary conditions for a sound relationship that benefits both parties.
In addition, a company must be certain that the supplier knows how to efficiently manage inventory. And the supplier must have the technical capability to perform VMI. Its computer systems and programs need to be compatible with the partner company to enable the necessary information exchange to execute VMI.
Simplify the chain by consolidating shipments
Managing a supply chain can get complicated quickly. From the OEM standpoint, the more Tier 1 suppliers that are involved, the more time someone must spend coordinating them. Many companies try to minimize the number of suppliers they use.
For example, consider a restaurant’s dependence on food distributors. The burger joint down the street needs many separate items to prepare and serve a meal consisting of a cheeseburger, fries, and drink. If the restaurant uses a different supplier for each component, imagine the traffic jam of delivery trucks that’d amass around the facility!
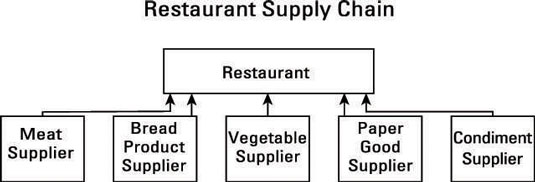
In the restaurant business, supply chains no longer rely on multiple suppliers with specialty support. All-in-one restaurant supply companies have emerged to simplify the material management process for restaurants. This new Tier 1 supplier purchases core supplies from specialty suppliers (now Tier 2 suppliers) and delivers them in one shipment to the restaurant.
Reducing the complexity of the supply chain eases the burden on restaurant management to keep ingredients and supplies in stock, and, because fewer trucks are making deliveries, this simplification decreases traffic congestion at the facility and the number of deliveries the restaurant must receive.
Another method for simplifying a supply chain, cross-docking, reduces a company’s inventory levels and the need for warehouse space. Cross-docking is a logistics network approach used to minimize warehousing costs and reduce inventory. This is a popular process for big retailers and grocery store chains.

The OEM maintains a shipping dock where supplier trucks arrive and park. The trucks are unloaded, and instead of placing the inventory in a storage warehouse, the goods are placed directly on the firm’s truck (or another supplier’s truck), which delivers the inventory directly to the facility. The end delivery truck may contain goods from multiple suppliers.
Cross-docking reduces pipeline inventory and also the need for warehouse space. It functions similarly to the simplified restaurant supply chain, but cross-docking leaves direct control over suppliers in the hands of the OEM instead of an all-in-one middleman supplier.
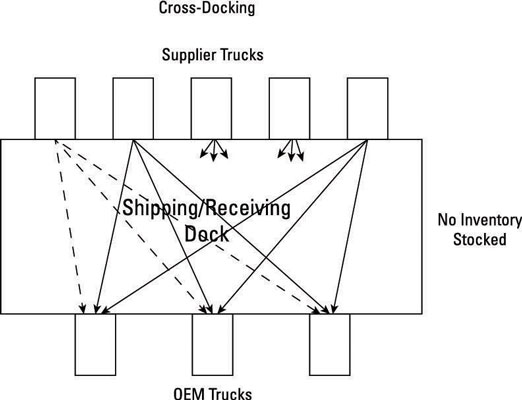