Solving problems the Six Sigma way requires varying degrees of skill in applied statistics. Solving complex problems requires considerable statistical expertise, but dealing with moderate problems or routine work takes less skill.
In Six Sigma, the highest level of statistical skill is called Black Belt, the medium skill level is Green Belt, and the everyday level is Yellow Belt. The nearby sidebar explains where the belt terminology came from.
The martial arts connotation really does make sense. A Six Sigma Black Belt is so expertly skilled and so experienced that she understands the true nature of her opponent (an underperforming process), and she knows how to apply the right skills and tools with grace and minimal effort to channel its energy and fully achieve the organization’s goals.
Although the Belt terminology is universally understood, it’s not universally accepted. Many companies and industries apply it as a broad standard, but the nomenclature is downright unfashionable in some circles.
Six Sigma roles
In the early 1990s, Motorola was assisting Unisys in solving complex problems associated with the production of large-scale multilayer printed circuit boards for military applications. They found the solutions by applying the advanced statistical analysis tools of Six Sigma.
The managers wanted to promote the value of the expertise developed within the team. One evening, while unwinding after a long day’s work at the Unisys facility in Salt Lake City, they hit on the idea of calling these engineers Black Belts — a term that captured the mystique of their discipline and skill. “Now that’s a name I can sell!” proclaimed the Unisys manager.
And it did sell. As the Six Sigma methodology flourished, so did the title of Six Sigma Black Belt as the master of statistical problem-solving. Later, as the need for lesser degrees of skill was identified, the terms Green Belt and Yellow Belt were added.
Across the global Six Sigma landscape, you can also find additional variants, including Blue Belt, Brown Belt, and even White Belt. You’ll even hear jokes about Chartreuse Belts, Polka-Dotted Belts, and more.
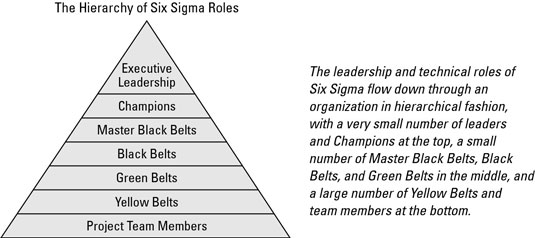
Master Black Belts
Master Black Belts (MBBs) are the trainers. They’re accomplished Black Belts with teaching skills — hands-on experts who teach and mentor Black, Green, and Yellow Belts and who often own the Six Sigma training curricula and Six Sigma knowledge content for their organizations. As mentors, MBBs consult other Belts on fundamental business issues as well as specific project application issues, challenges, and problems.
Black Belts
Black Belts are the most highly trained experts in the complete set of Six Sigma methods and tools. They’re highly respected for possessing the knowledge and skill required to facilitate breakthrough-level improvements in the most complex of processes. Black Belts typically comprise 1 to 2 percent of the organization and work full-time leading Six Sigma projects. The Black Belt
Implements Six Sigma projects that historically are advertised to return a bottom-line value of $150,000 or more to the organization. A Six Sigma Black Belt may implement as many as four such projects a year.
Mentors and coaches others in applying Six Sigma methods and tools.
Leads complex departmental, business unit, or cross-functional process improvement projects that require significant data and analytical skill.
Disseminates new strategies and tools through training, workshops, case studies, local symposia, and more.
Discovers internal and external (suppliers and customers) opportunities for new Six Sigma projects.
Green Belts
The Six Sigma Green Belt is trained and skilled to solve the majority of process problems in both transactional and manufacturing environments. Green Belts are process leaders, process owners, professional staff, operational specialists, managers, and executives who have a significant degree of business, leadership, statistical, and problem-solving skills.
Green Belts typically make up 5 to 10 percent of the organization and work part-time, either in support of Black Belt projects or leading less-complex projects of their own. The Green Belt
Implements about two projects per year that historically are advertised to return an average bottom-line value of $35,000
Teaches local personnel to apply Six Sigma strategies and tools and coaches local personnel through one-on-one support
Leads departmental, business unit, or cross-functional process improvement projects in environments that don’t require complex data or heavy statistical analyses
Disseminates new strategies and tools via training, workshops, case studies, local symposia, and more
Discovers internal and external (that is, suppliers and customers) opportunities for Six Sigma projects
Yellow Belts
All members in the organization can apply elements of the Six Sigma methodology and improve their work environments. Everyone can assist Green Belts and Black Belts in completing projects. But not everyone needs to be immersed in the details or challenges at a Green or Black Belt level.
The Six Sigma Yellow Belt is this “everyone else.” Yellow Belts are staff members, administrators, operations personnel, project team members, or any other technical or nontechnical position. Nearly anyone can identify measurement scales, define critical process factors, collect some data, characterize a process, make easy improvements, and cultivate opportunities.
The goal of Yellow Belts is to think in a data-driven, cause-and-effect process manner and apply this thinking to their areas of work. Yellow Belts support Black Belt and Green Belt projects and can even take on small projects of their own.