Filament drive mechanisms can be machined in a variety of ways. Look for even, well-cut drive teeth that grip but don't strip or grind through your filament. Too-sharp teeth can be as bad as too-blunt teeth.
Filament drives used in thermoplastic extruders perform the same job but are manufactured in various ways. At the top of the figure is a traditional hobbed-bolt filament drive, which is the most common type of filament drive; it performs adequately. In the middle is a professionally machined drive wheel, which usually provides the most grip around the filament as it's pushed into the extruder. This wheel is usually mounted directly on the shaft of the extruder motor or on a gearbox attached to the motor. At the bottom is another machined bar with shallow, blunt grooves; this design won't grip as firmly as either of the top or middle drives shown.You can assemble an extruder in several ways. In the simplest assembly, the filament drive wheel fits directly on the shaft of the extruder's stepper motor and drives the filament directly via rotation of the motor shaft. This method provides the lowest torque but requires the fewest other components.
The most basic filament extruder can perform adequately if you have a powerful drive motor and well-machined hot-end to reduce the forces required to push the filament. On the left side of the following figure is the same professionally machined drive wheel shown earlier. On the right side is another direct-drive motor, but with only a basic drive cog with a groove for the filament; it won't have as much grip as the one shown on the left.
This cog costs little to manufacture but also has the lowest drive performance. A direct-drive motor has no gearing to improve torque, so you should avoid this type if at all possible. Direct-drive extruders do have one advantage: Two of them can be placed close together to provide dual extrusion.
A compact gearbox can be attached to the output of a stepper motor to greatly improve the torque and rotational resolution compared with the direct-drive extruders (see the following figure). The gearbox can be compact to allow for dual extrusion.
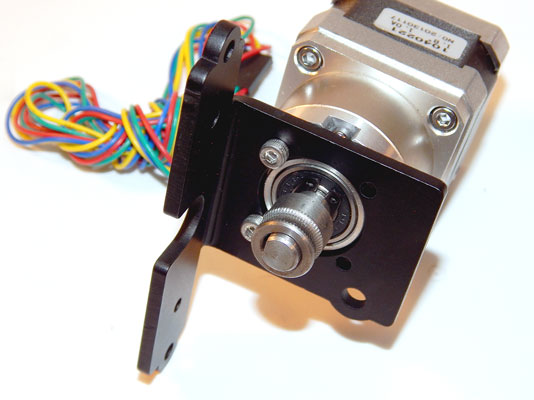
Many enhancements in extruder drive mechanisms have been developed in recent years. One of the most successful is the dual-grip system, shown in the following figure. The advantage of a dual-grip system is that the round filament is gripped and pushed from both sides instead of being pressed flat on the idler side (which usually squashes it onto a metal rotating bearing). More manufacturers are switching to a dual-drive gear system, which increases grip on softer filaments such as ThermoPlastic Urethane (TPU) rubber and helps drive harder or slippery materials faster.
In RepRap 3D printers, it's still common for the motor to be connected to a series of 3D-printed gears (see the following figure). The gearing allows the motor to turn quickly while the drive mechanism turns slowly, thereby increasing the torque and allowing the filament to be driven with increased force and precision into the hot-end. This arrangement provides fast printing and retraction with less chance of material becoming jammed due to lack of torque.

Another common type of extruder is the Bowden, which works on the same principle as the brake-lever cable of a bicycle. A slippery Teflon (PTFE) tube separates the extruder drive motor from the hot-end. This tube allows the driven filament to be constrained and pushed into the hot-end section.
The Bowden extruder is often used in small or lightweight machines because it offers several advantages:
- The design removes the bulk, mass, and weight of the motor from the moving carriage, leaving only the hot-end.
- More hot-ends can be mounted on one 3D printer.
- The design can be ideal for machines with a lightweight head that moves quickly.
- The design has more parts and complexity compared to a non-Bowden design.
- The printer must perform a longer filament retraction after every print move to minimize oozing due to the pressure and spring that occur when the filament is pushed down the tube.
- The design can be hard to control and tune.