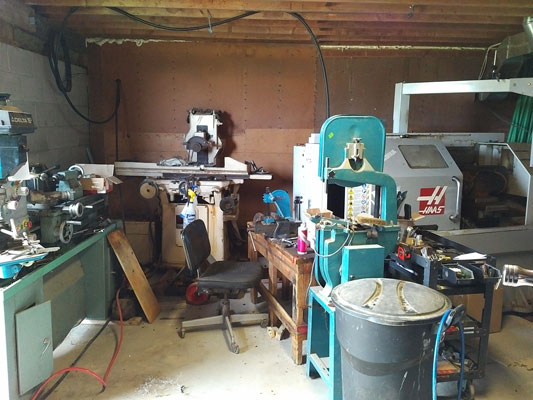
Perhaps you're comfortable working in these conditions, but do you expect potential customers to bring their business here?
Granted, no one particularly looks forward to making the bed every morning or washing the dishes after dinner, yet it's something most of us do before inviting guests over for a party. And that's exactly the attitude that should be taken in a precision machine shop: Every day is a party, and the guests (your customers) will be arriving at any time.
It's more than appearances, though. Machine tools are expensive and should be treated as such. Good housekeeping goes well beyond keeping the filters clean or checking for axis wear. It's a culture, one in which everyone is proud of his or her workplace and participates in its upkeep. The term "the floors are clean enough to eat off of" might be an exaggeration, but it doesn't have to be, at least not much of one. (See the following figure for proof.)
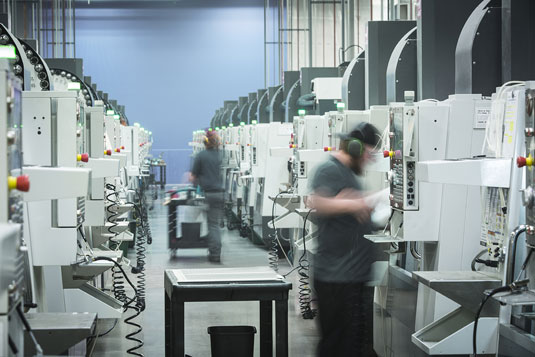
Many machine shops and manufacturing companies "get it," and are clean, well-organized, and forward-thinking.
Cleanliness is also about safety. The vast majority of shop owners and managers care about their employees, and investing in air filtration systems and a "smog hog" for each CNC machine might seem prohibitive, but it's far better than hearing one day that Wayne has lung cancer or Jim was diagnosed with emphysema, and wondering if dirty shop air was the culprit.
No one wonders about the risks of slippery floors or lifting heavy objects — both are obvious, and everyone takes care to avoid them. But so too should they avoid letting the shop reach 90 degrees in July. Not only will insufficient air conditioning jeopardize part quality, but also employee retention as well. The same holds true for overly cold temperatures in the winter. Keeping the shop at a consistent temperature year round is less expensive than remaking scrap parts or training new employees, never mind the benefit to its CNC machines.
Without beating a dead horse, successful manufacturing companies embrace employee safety, cleanliness, air quality, and all the things that make a shop environment pleasant to work in. Equipment lasts longer. Employee morale is better than in "piggy" workplaces. Visiting customers spread the word to others, "I've never seen such a clean shop; they must really have their ducks in a row," (yes, some people really say this), thereby increasing the likelihood of new business. Dirty, hot, dangerous shops? There's really no reason for it. Get sweeping.
Lean manufacturing principles mandate a clean, well-organized shop. It's called 5S, and it stands for seiri, seiton, seiso, seiketsu, and shitsuke. Roughly translated, the five S-words are Sort, Set, Shine, Standardize, and Sustain. If you want a shop you can be proud to show off to visitors (and one that's a joy to work in), this is a good place to start.