The complementary measurement of yield for Six Sigma is defects. When a process or characteristic doesn’t perform within its specifications, it produces a noncompliant condition, called a defect. If your yield is 90 percent, you naturally must have 10 percent defects.
Defects equal failure
When a process or characteristic doesn’t perform within its specifications, it is considered defective; in other words, it produces a noncompliant condition called a defect.
Automatically defining a defect as a noncompliance with specifications may seem overly simplified. Just because a characteristic exceeds a specification doesn’t necessarily mean that the system it’s part of will break or stop functioning.
Defects per unit
Six Sigma applies to all areas of business and productivity — manufacturing, design, sales, office administration, accounts receivable, healthcare, finance, and so on. Each of these areas works on and produces different things — products, services, processes, environments, solutions, among others.
To bridge these diverse disciplines, in Six Sigma you call the thing you’re working on a unit. A unit may be a discretely manufactured product or an invoice that crosses your desk. Whatever it is you do, in Six Sigma it’s called a unit.
A basic assessment of characteristic or process capability is to measure the total number of defects that occur over a known number of units. You then transform this measurement into a calculation of how often defects occur on a single unit, like this:

where DPU stands for defects per unit.
For example, if you process 23 loan applications during a month and find 11 defects — misspelled names, missing prior residence information, incorrect loan amounts — the DPU for your loan application process is
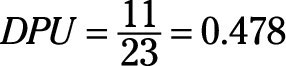
That means that for every two loans that leave your desk, you expect to see about one defect.
Defects per opportunity (DPO) and per million opportunities (DPMO)
A DPU of 0.478 for an automobile is viewed very differently than the same per-unit defect rate on a bicycle. That’s because the automobile, with all its thousands of parts, dimensions, and integrated systems, has many more opportunities for defects than the bicycle has. A DPU of 0.478 on an automobile is evidence of a much lower defect rate than the same DPU on a simpler product.
The key is in transforming the defect rate into terms that are common to any unit, whatever it is or however complex it may be.
How to deal with DPO
The way to level the playing field so you can directly compare the defect rates of systems with very different complexities is to create a per-opportunity defect rate, known as defects per opportunity (DPO). The common ground between any different units is opportunity.
Examples of opportunities include the following:
In a product, the critical dimension of diameter on an automobile axle
In a transactional process, the applicant’s mailing address on a loan approval form
In a hospital, getting the correct medical history records into the patient’s file
In the design of a retail store environment, the placement of clearance sale racks
In a manufacturing process, the tightening of a bolt to the correct torque
The number of opportunities inherent to a unit, whatever that unit may be, is a direct measure of its complexity. In fact, when you want to know how complex a unit is, you count or estimate how many opportunities for success or failure exist. Sometimes, opportunities are individual characteristics that are critical to the system’s performance. Other opportunities are characteristics that have a specification.
Use the following formula to calculate DPO:

With a calculated DPO measurement, you can now fairly compare how capable an automobile is to how capable a bicycle is. For example, you may observe 158 out-of-specification characteristics on an automobile. After some study, you also determine that the number of opportunities for success or failure within that automobile is 14,550. Its DPO is then
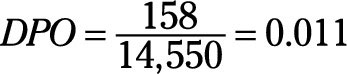
For a bicycle, on the other hand, you may find only two non-compliant characteristics among its 173 critical characteristics. So its DPO is
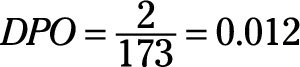
Even though an automobile and a bicycle are two very different items with very different levels of complexity, the DPO calculations tell you that they both have about the same real defect rate. But you observe more defects on the automobile, because that item has many more opportunities for defects.
How to address larger and accumulated units with DPMO
When the number of opportunities on a unit gets large and the number of observed defects gets small, calculated DPO measurements become so small they’re hard to work with. For example, two commercial airline crashes (defects) observed out of 6 million flights in a year translates into

Although 0.000000333 is fortunate, it’s definitely an inconvenient number to work with! Additionally, you may also want to estimate out into the future to know how many defects will pile up after running the process or observing the characteristic for a long time. After all, DPU and DPO look only at a single unit or a single opportunity.
A simple way to solve both of these problems is to count the number of defects over a larger number of opportunities. For example, how many defects occur over a set of one million opportunities? This defect rate measurement is called defects per million opportunities and is used very frequently in Six Sigma. In fact, Six Sigma is famous for its defect rate goal of 3.4 defects per million opportunities.
When a process is repeated over and over again many times — like an automobile assembly process, an Internet order process, or a hospital check-in process — DPMO becomes a convenient way to measure capability. When calculating DPMO, you don’t want to actually measure the defects over a million opportunities. That would take way too long. Instead, the way you calculate DPMO is by using DPO as an estimate, like this:
DPMO = DPO × 1,000,000
This setup also means you can track backward, going from DPMO to DPO:
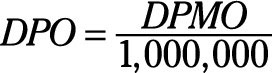