Information about product cost helps managers to set and adjust prices and to decide how to best utilize limited production capacity. Here you use only two credit accounts: Accounts payable (which are moneys owed to suppliers), and Wages payable (moneys owed to employees). To increase one of these credit accounts, credit it to the right. To decrease it, debit it to the left.
Here’s the premise of the example you're about to walk through: fictional National Snow Globe Corp. manufactures custom souvenir snow globes for tourist gift shops. The company makes snow globes in large batches. Each globe features a unique three-dimensional image inside, a custom logo, and one of four different grades of snow.
Purchase raw materials.
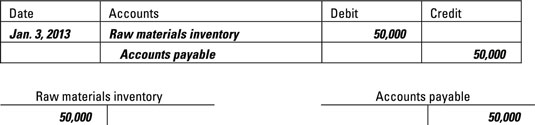
On January 3, National Snow Globe purchased $50,000 worth of raw materials on account. You debit Raw materials inventory for $50,000 and credit Accounts payable for $50,000.
The debit to Raw materials inventory (a debit account) increases that account’s balance; the credit to Accounts payable (a credit account) increases that account’s balance.
Pay for direct labor.
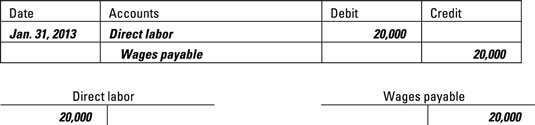
On January 31, National Snow Globe recorded payroll for direct labor amounting to $20,000. Over this time period, employees worked 2,000 hours. You debit Direct labor for $20,000 and credit Wages payable for the same amount.
The debit to Direct labor (a debit account) increases that account’s balance; the credit to Wages payable (a credit account) increases that account’s balance.
Pay for overhead.
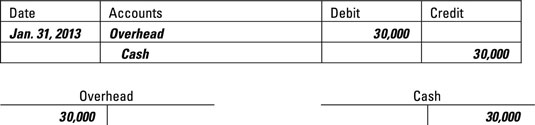
Overhead costs are all product costs not included in direct materials and direct labor. They typically encompass indirect materials, indirect labor, property taxes on the factory, depreciation of factory equipment, factory maintenance, and the cost of factory supervision.
On January 31, National Snow Globe paid $30,000 for overhead. You debit Overhead for $30,000 and credit Cash for this amount.
Requisition raw materials.
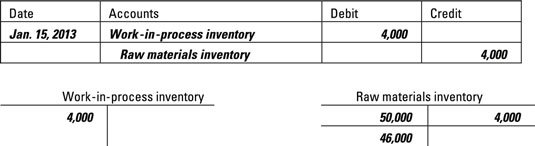
The Work-in-process inventory account accumulates all direct materials, direct labor, and overhead costs that a company puts into production.
On January 14, National Snow Globe received an order from the Johnny Gentile Library and Museum in Jupiter, Florida, for 5,000 snow globes. The factory manager numbered this job BRM-10.
On January 15, Supervisor Jane Smiley arrived at the warehouse with a materials requisition slip for job BRM-10, requesting that workers put $4,000 worth of raw materials into production. Logistics personnel delivered the goods to Jane’s department. Jane then notes receipt of the goods on the job order cost sheet.
You debit the Work-in-process inventory account and credit Raw materials inventory for $4,000.
Because of a previous transaction, the company already had $50,000 in its Raw materials inventory account. After this transfer shifts $4,000 from Raw materials inventory into Work-in-process inventory, the company has a remaining balance in Raw materials inventory of $46,000.
Utilize direct labor.
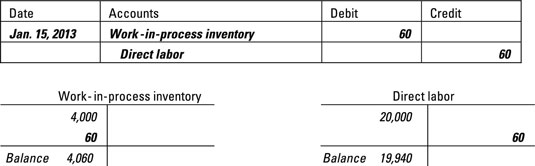
Amanda Carpa, an employee in Jane Smiley’s department, spent six hours working on job BRM-10. Jane then notes the cost of hours worked by Amanda on the job order cost sheet. At the end of the day, she completes a time ticket. The company pays Carpa $10 per hour, so the total direct labor cost for six hours equals $60 (6 hours x $10 per hour).
The journal entry debits the Work-in-process inventory account and credits Direct labor for $60.
Add up total overhead. Identify one or more cost drivers. Compute the overhead allocation rate for each cost pool.

National Snow Globe estimated that overhead would amount to $30,000 for the month.
The company evaluated its overhead, identifying two appropriate cost drivers. The company recorded $10,000 in a cost pool called Utilities. Managers determined that the appropriate cost driver for this cost pool should be direct labor hours; the activity level for this pool is 2,000 hours.
The company also recorded $20,000 in a cost pool called Setups. Management determined that the appropriate cost driver for this cost pool should be the number of setups, estimating that it would have a total of 50 setups during the month.
Divide estimated overhead in each cost pool by its cost driver activity level. For example, in the Utilities cost pool, the company expects to incur $10,000 worth of overhead. The company also expects to have employees work 2,000 direct labor hours.
Therefore, the overhead application rate comes to $5 per hour. Each direct labor hour also comes with $5 worth of overhead. Similarly, the overhead cost pool for setups comes to $20,000, and the company plans to do 50 setups. Therefore, the company assigns $400 worth of overhead for each setup.
Apply overhead.

To figure out the overhead assigned to job BRM-10, measure the activity level of each cost driver and then multiply it by its respective overhead allocation rate.
Because six hours of direct labor were expended to make BRM-10 and the overhead allocation rate for utilities is $5 per hour, assign $30 in overhead cost to BRM-10. The job entailed one setup (at an overhead allocation rate of $400 per setup), so assign another $400 worth of overhead to this job. Therefore, BRM-10 gets assigned a total of $430 worth of overhead.
As soon as the company’s accountants are able to estimate overhead assigned to the job, they add this cost to the job’s job order cost sheet.
Create the journal entry to allocate overhead.
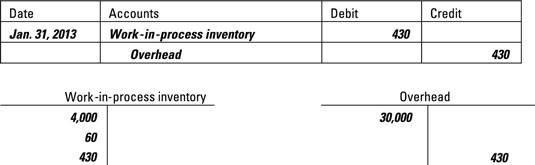
Debit (increase) Work-in-process inventory and credit (decrease) Overhead. This entry effectively moves the overhead cost of the products out of the overhead pools and into the cost of the goods that you make.
After you finish manufacturing the goods, add all the costs of making BRM-10.
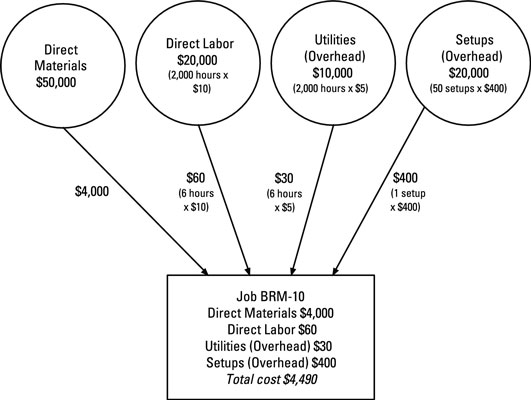
Remember to include direct labor, direct materials, and overhead costs, so that the total cost of job BRM-10 sums to $4,490.
To record that you finished making the goods, transfer this cost from Work-in-process inventory to Finished goods inventory by debiting (increasing) Finished goods inventory and crediting (decreasing) Work-in-process inventory.
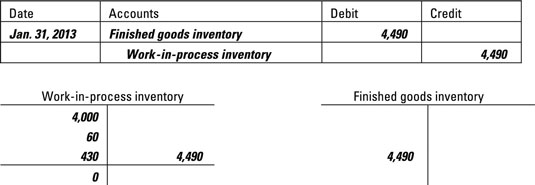
Note how transactions in the books reflect what happens in the factory. As the goods are moved off the assembly line and into the finished goods warehouse, the accountants take their cost out of the account Work-in-process inventory and into the account Finished goods inventory.
Check out the completed job order cost sheet for BRM-10.
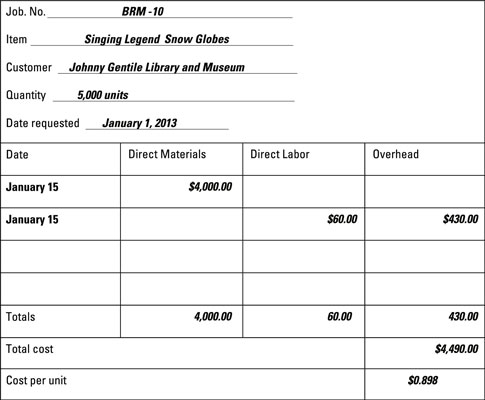
The job order cost sheet for BRM-10 illustrates how the company keeps track of direct materials, direct labor, and overhead costs throughout the production process.